Insurance allows individuals and organizations to exchange the risk of a large loss for the certainty of smaller periodic payments, known as premiums. The exchange (or transfer) of risk is laid out in a legal contract called the insurance policy, which spells out the coverage, compensation, and/or other benefits.
Generally speaking, premium rates are driven up and down by the anticipated cost of claims losses. When real-world risks (e.g., fire, windstorm, litigation,) and their attendant costs (e.g., labor, construction materials, and judicial verdicts) are rising, insurers are forced to factor these increasing costs into future policyholder premiums. For most economic goods, the cost of the product to the business is known at the time the customer is given a price and the customer purchases the product/service. However, for insurance products, the actual cost of providing coverage is unknown to the insurer for some time. Nonetheless, the insurer remains obligated to pay covered claims in the face of this uncertainty, even if the premium it received turns out to be wholly inadequate.
Premiums are fundamentally derived from projected cost of claims (losses) and other expenses. While each insurance company’s operational expenses vary, they are relatively predictable. Claims costs, on the other hand, are not always predictable. Insurers use statistics and historical loss information to forecast an accurate estimate of the amount of losses to be paid in the future — sometimes the distant future — for a particular pool of risks. The accuracy of the estimate depends on the type of risk, policyholder characteristics, and the size of the pool. The home insurance policy premium reflects many characteristics of the property, including age of the home, property attributes, and building materials.
Risk has two key dimensions — frequency and severity — and both help determine insurability.
“Frequency” relates to how often a loss occurs, i.e., whether the risk/event is common or relatively rare. For example, older homes tend to develop problems in the areas of electrical wiring, plumbing, roofing, and foundation more frequently than newer ones. Therefore the potential for loss would be greater and that would need to be accounted for in the premium.
“Severity” relates to how costly losses resulting from that risk could be, i.e., whether they could be relatively inexpensive or truly catastrophic in nature. For example a steel beamed, poured concrete home is less likely to burn than a wood frame structure. However, a wood frame home is less likely to sustain damage during earthquakes.
As you can see, the construction of a home is an important factor that should be considered when evaluating a risk. Details about the building, including construction type and materials used, are important for insurance professionals to understand so that they can properly educate consumers about rating, premium, and risk management /mitigation options.
Most people understand the basics of the building process. It starts with the floor plans being developed, building site cleared and permitting complete, the actual construction of a home can begin. Typical construction begins by excavating the land and pouring the concrete for foundation and footers. Building the exterior walls and main load-bearing structure will occur following by the ceiling and wall framing being installed. Outer walls will be covered with sheathing and a water protective barrier. Once roof and exterior wall covers are added, windows can be installed, interior walls framed, and utilities, such as plumbing, electrical, gas, and HVAC, are added to the structure. Installation of insulation and interior drywall to complete walls and ceilings begins. Final plumbing and electrical fixtures as well as floor wall and ceiling covers are added and major appliances installed. The house is then ready for the owners to move in and make a home!
What some people don’t realize is that the type of construction, age of the home (with age comes wear and tear and possible claims) and quality of construction all factor into home insurance premium rate. One of the largest factors related to this is the type of construction of the building. Property risk is assessed by its relative flammability and destructibility by covered perils. Whether a home and other structures are made of wood, stucco siding, brick, concrete, or steel frame construction can factor into burn rate in case of fire or the ability to withstand high winds in a storm. In addition to the premium, construction is an important aspect an underwriter considers when evaluating an application for insurance.
As construction of a home is an important factor that should be considered when evaluating a risk, it is important for insurance professionals to have a basic understanding of building construction, materials involved, and terminology.
Let’s start with the basics and work our way up and around. The structure of the home includes the foundation as well as the floors, walls, and roof. In this chapter we will review the purpose of the structure and identify structural elements.
Foundation
Foundations are the supportive structures on which all houses are built. The type used depends on a property’s age, local codes, and the type of ground on which it stands.
Crawlspace A crawlspace elevates the living space off of the ground, which is beneficial in termite-prone or damp regions. It allows a place and easy access for ductwork and pipes. It is less expensive than a full basement.
Basement Basements are usually built on a concrete slab, and a basement is actually a taller version of a slab. A footing is poured and foundation walls are constructed of poured concrete or a concrete block can be set on top.
Slab A concrete pad, reinforced with steel, covers the area on which the house sits. In some cases the edges of the slab, directly below the exterior walls, will be thicker than the rest of the slab. Modern slab foundations are well insulated.
Pile and Girder The walls are supported by a column of reinforced concrete, or steel, drilled into the ground. The depth and frequency of beams depend very much on the type of ground below the building, and the building size. Piles may also be required for internal loadbearing walls.
Framing of the residential structure is one of the most important aspects as it serves as the “skeleton” of the building.
Wall Systems
Two types of wall systems/framing we will discuss are masonry and wood frame.
Masonry construction has exterior walls made of non-combustible materials. It is a highly durable form of construction and is the building of structures from individual units laid in and bound together by mortar. The common materials of masonry construction are brick, building stone such as marble, granite, travertine, and limestone, and concrete block. The materials chosen are laid using mortar between the individual units. The mortar binds the individual units together and also provides protection from air and water getting through the joints. Advantages of masonry construction include it is harder to ignite, consumed more slowly by fire, and more structural stable in the event of a storm.
Wood frame construction has exterior and interior walls, floors, and roofs made of wood or other combustible material. Upper floors are wood, but the ground floor may be wood or concrete.
It is the most common building methods. Vertical and horizontal framing members are assembled and nailed together to provide the structure needed to affix finished coverings to. Wood framing is more light weight than masonry and quicker and less expensive to install.
Roof Systems
A roof system is the structure that forms the covering on the uppermost part of a building or shelter which provides protection from animals and weather, notably rain or snow, but also heat, wind and sunlight. Most roofs are angled to divert rainwater away from a house. The roof system may be made up of a wood frame roof built on-site or a prefabricated truss roof in which major components are constructed in a factory and then assembled on-site.
The shape of roofs differs greatly from region to region. The main factors which influence the shape of roofs are the climate and the materials available for roof structure and the outer covering. Common roof shapes include:
Gable The gable roof is characterized by the triangular wall shape formed where the pitched roof surfaces meet along an apex known as a ridge. This design creates a greater attic area than a comparable hipped roof design.
Hip On a hipped roof, the gable is effectively cut back at ridge level to provide a triangular sloping roof. The angled ridge that joins this section with the main roof is called a hip.
Flat A flat roof looks level, but has a slight pitch to allow water to run off the surface. This design is often used on ground-floor extensions, but may form the main roof structure for some houses.
When building closer to a coast line or other area where concerns of potential wind damage exist, additional requirements may be required. For example, in Florida building requirements require hurricane clips and straps. These secure the roof framing to the wall framing and provide additional support to anchor the roof structure to prevent uplift during a storm. Existence of hurricane straps or clips may result in premium discounts for an applicant.
Once the skeleton of the structure is complete, it is covered with sheathing. Sheathing ties together the wall and roof framing and contributes to the strength of the structure. It also provides a solid nailing surface for exterior finishes and roofing materials. Common types of sheathing include:
- Plywood
- Oriented strand board (OSB)
- Rigid foam panels
- Exterior gypsum board
Roof Construction
The purpose of the roof is to protect the building from exterior elements such as animals or weather. We mentioned that the roof structure may be made up of a wood frame roof built on-site or a prefabricated truss roof in which major components are constructed in a factory and then assembled on-site. It is then enclosed with sheathing and is ready for the final roof covering. There are several different types of roofing materials which we will review now.
Composition Shingles
Composition shingles, or asphalt shingles, are the most common roofing material used. They are made using asphalt coated felt paper or fiber mat that has been covered by a granular material. Shingles are classified by the manufacturer’s warranty: typically known as 20-year, 25-year, or 35-year shingles. Shingles may last longer than the warranty period. The warranty period, therefore, is not a guarantee of the useful or service life of the shingles as they are impacted by exposure and slope. Sunlight will wear shingles, and areas of direct sunline with wear out fastest. The steeper the roof, the longer the shingles should last.
Concrete or clay tile
Concrete or clay tiles are a high quality roof covering. Life expectancy of a concrete or clay tile roof could be 50–100 years. This type of roof covering is very heavy and requires a roof framing that can support that load. Tiles are either nailed in place or are secured with special clips or ties. In some regions they are mortared in place. Concrete and clay tile can be found in different shapes and sizes.
Metal Roofing
Metal roofs can be made of materials such as copper, steel, stainless steel, or aluminum. They come in sheets or shingles. They can be stamped or finished to replicate the look of stone, painted or coated, or have granules imbedded in the finish. Sheets of metal roofing are connected using seams which interlock the panels together. Seams can be crimped or soldered.
Wood Roofing
There are two classes of wood roofing: shingles and shakes. Wood shingles are machine cut to ensure uniform size and are generally smaller and thinner than shakes. Wood shakes are hand cut or split and vary in size. Surface areas of a wood shake may be uneven. The life expectancy of a wood roof will vary and is impacted by exposure to weather, slope, grade of shingle, and the amount of shade and sun. Excess sunlight can dry out the wood resulting in excessive wear, excess moisture can result in rot or moss growth.
Rolled Roofing
Rolled roofing is made of the same material as composition (asphalt) shingles and typically found in rolls that are 18 or 36 inch wide. This roofing material is installed in long, overlapping strips. This roofing material is usually found on flat or low slope roofs. This is generally a low quality roofing material and has a limited life expectancy of five to ten years.
Built-up Roofing
Built-up roofing is also referred to as tar and gravel. It is a multi-layer roofing system which consists of a vapor barrier, insulation, membrane (felt layers), and a surfacing material such as gravel, although a gravel top coat is not required. The number of felt layers is referred to as the ply. This type of roofing can be referred to as two, three, four, or even five ply. Built up roofing is found on roofs with a flat or low slope.
Regardless of the roof covering, damage of the roof can exist and should be evaluated for any damage. Worn, cracked, loose or missing roofing material can result in leaks. Interior leaking can occur at joints or intersections on the roof. Flashings are installed on the roof where materials meet, where the roof changes direction or where the roof interests a wall. The purpose of flashings is to keep water out. If flashings are installed incorrectly or are missing, interior leaking can result.
Chimneys
A chimney is a structure which provides ventilation gases or smoke from a fireplace, stove, or furnace. They can be constructed of masonry or metal. Masonry chimneys can be lined or unlined. Improper installation or maintenance can result in chimney fires. Metal chimneys could rust as a result of water.
Exterior finishes
Once the wall framing is complete and sheathing installed, the exterior of the home is ready for the exterior cladding or finishes. The exterior finish chosen will depend on the home construction, location (climate) of the structure, cost, and of course personal preference.
Siding
Siding forms the outer layer providing waterproofing and a decorative effect for the home. Siding panels can be installed horizontally or vertically. Siding can be found in many types of materials including wood, metal, vinyl, and fiberboard.
Wood siding
Wood siding is available in clapboard, planks, or shingles. Clapboard is installed horizontally, overlapping wood clapboard. Wood plank siding is installed vertically and can be board and batten, board on board, or tongue and groove. Wood plank siding can also come in a plywood version and often referred to as T1–11. Wood shingles are similar to those we reviewed when we discussed roofing.
Wood siding is not a good exterior finish in fire prone areas as windborne embers could ignite the exterior wall coverage and spread to other areas of the home and result in substantial damage. The exception to this would be if the siding is made of a fire-retardant-treated wood. Wood siding does require regular maintenance to ensure rot or other deterioration does not occur which could result in damages to the structure.
Metal siding
Metal siding is a durable exterior finish that can come in a variety of colors and styles and usually constructed of aluminum or steel. Metal siding is sold in strips that fasten to the exterior wall and then to one another to create a waterproofing finish to the exterior of the structure.
Aluminum siding is susceptible to denting and is not recommended for high hail areas. Steel siding is less likely to dent, but will rust if the finish is removed.
Vinyl siding
Vinyl siding is a low cost exterior finish, which like metal siding, is sold in strips that fasten to the exterior wall and then to one another to create a waterproofing finish to the exterior of the structure. It comes in a wide array of colors and textures. It can become brittle in cold weather, is susceptible to cracking if struck, and will melt and warp if exposed to the high temperatures associated with a wild fire.
Fiberboard
Fiberboard siding is a low maintenance product which can come in different colors and textures. It is sold in panels and installs similar to wood siding. It is not subject to insect damage or rot like wood siding.
Stucco
Stucco as an exterior finish is a mixture of cement, lime, aggregate and water that is applied to the exterior of the building in a thin coat, typically a two or three step process depending on the framing. If applied to wood framed walls, a three coat process is required to build up the thickness. If stucco is applied to masonry walls, only a two coat process is require as the masonry is such a strong substrate the additional thickness is not required. When stucco is applied over wood framed walls, it is susceptible to cracking since the wood frame walls will expand and contract with changes in temperature and humidity. Cracking in the stucco could result in deterioration due to moisture exposure.
Masonry or Masonry Veneer
Masonry is the building of structures from individual units laid in and bound together by mortar. The common materials of masonry construction are brick, building stone such as marble, granite, travertine, and limestone, and concrete block. The materials chosen are laid using mortar between the individual units. The mortar binds the individual units together and also provides protection from air and water getting through the joints. Advantages of masonry construction include it is harder to ignite, consumed more slowly by fire, and more structural stable in the event of a storm.
Masonry Veneer consists of masonry units installed using metal strips on a structurally independent wall usually constructed of wood or masonry. Masonry veneer is not structural, but is primarily used as a decorative affect.
Interior finishes
The interior finishes of a house can be an indicator of building quality and home maintenance. Selected interior finishes could increase the overall replacement cost of a building and should be reviewed.
Flooring
Floors provide a durable walking surface within the home. The choice of material for floor covering is affected by factors such as cost, endurance, noise insulation, comfort and cleaning effort. Materials can be classified carpet, resilient flooring, wood flooring, ceramic tile, or stone.
Carpet
Carpet is constructed of synthetic or natural fibers which are woven together with a backing material. Common materials of carpet fiber include polypropylene (Olefin), nylon, acrylic, or wool. Carpet is an economical flooring option and is very versatile as it comes in a wide variety of colors and styles and can cover many different substrates and on all grade levels. Carpet quality is gauged based on the fiber type, weight and constructions of the carpet, and the type of underpad.
Resilient
Resilient flooring, including vinyl, rubber, cork, and linoleum, is installed in sheets or tiles. It is usually installed over a plywood underlayment. It is generally thin but higher end products could include a cushioned backing. It is durable flooring that is very flexible and inexpensive.
Wood
Wood flooring can generally be divided into three types: hardwood, engineered and laminate.
Hardwood floors can be constructed of strips or parquets of oak, cherry, walnut, birch, mahogany, or maple. They are either nailed or glued in place. Hardwood flooring is either pre finished or finished on site. Although a highly durable floor surface, it can be susceptible to damage from termites, rot, fire, or water. Should hardwood floors become damaged, individual boards can be replaced and the floor surface area sanded and refinished.
Engineer wood floors are made of planks that have several layers, with a thin top layer which is made of hardwood that has been bonded to a base. Engineered wood floors are installed by snapping planks together creating a floating floor, or may be glued, stapled or nailed in place. Since the top layer is actual hardwood, it is possible to sand and refinish these floors but depends on the thickness of the hardwood layer.
Laminate wood floors is similar to engineered wood floors except the top layer is a clear laminate that is bonded to a decorative layer which is what gives it the look of wood floors. Laminate is not secured to the subfloor beneath it, but has a foam layer beneath it which acts as a water barrier. Laminate flooring cannot be sanded, stained or refinished.
Ceramic tile
Ceramic tiles are a high quality floor covering which are resistant to most normal wear and tear assuming they are properly installed and supported. Ceramic tiles are constructed of fired clay which is glazed or unglazed. Because they are resistant to water, they can be used in bathrooms and kitchens. Ceramic tiles are generally installed over a thin set of mortar or adhesive which joints between the tiles filled with grout.
Stone
Stone flooring is a natural material that is cut and laid into structures. It is strong and durable. Stone flooring must be finished and sealed to maintain their appearance and durability. Stone flooring can be constructed of granite, slate, marble, limestone, and travertine. Stone flooring is available in a variety of shads and colors, natural to the type of stone. The natural coloring may lead to varied shading throughout the floor surface. Stone thickness, hardness, and porosity affect the price and where it should be installed within the home.
Walls and Ceiling finishes
Just like exterior walls, interior walls can be made of a variety of materials. The two most common are plaster and drywall. In addition to plaster and drywall, wall finishes can include paneling, stone or tiles.
Plaster
Plaster is a mixture of gypsum that is applied to the wall surface with a trowel. Plaster, like stucco, is applied in layers. The wall surface that the plaster mixture is applied must have a type of backing material, referred to as lath, which the mixture can adhere to. Lath can either be made of wood, wire, or gypsum board (drywall).
Drywall
Drywall as a wall finish because popular in the early 1960’s and is currently used extensively. Sheets or sections of drywall are available in 4’x8’ sheets and typically sold in 3/8”, ½”, and 5/8” thickness. It is nailed or screwed to framing members with the seams between the sheets taped and filled with drywall compound. Drywall is often referred to as wall board, sheet rock, plasterboard, or even gyprock. Other versions of drywall are available which are more resistant to water or fire.
Cabinets and countertops
Cabinets and countertops, commonly found in bathrooms and kitchens, can be built from wood or fiberboard covered with a veneer. Quality of cabinets varies based on several aspects such as material used in construction, joints, and hardware.
Countertops can be made of a variety of products that have an impact on the cost, maintenance, and durability. Laminate countertops are made of fiberboard which is covered by a laminated plastic which can be made to look like natural stone or a solid color. It is inexpensive, easy to clean and maintain, and water resistant. It can be susceptible to cuts, chips, and heat. Natural stone, such as granite or marble, stainless steel, tile, or manufactured products are also used in countertops.
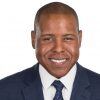
About Larry Nicholson
Director, Underwriting and Training at American Integrity Insurance Company VP, Board of Directors at Society of Insurance Trainers & Educators (SITE)
Director, Underwriting and Training at American Integrity Insurance Company
VP, Board of Directors at Society of Insurance Trainers & Educators (SITE)